En 2022, A. Lange & Söhne sigue fabricando piezas de excepción con un nivel técnico que nos sorprende y también innova con nuevos materiales. El Odysseus, que con su éxito tiene a la manufactura trabajando al máximo, ahora aparece en titanio. De hecho, fue el reloj monumental que la marca escogió para decorar su espacio de exposiciones en el salón Watches and Wonders 2022 de Ginebra.
¿En realidad cuál es el reto de fabricar alrededor de 5,000 piezas al año de todas sus colecciones y que se requiere? Pudimos hablar con Tino Bobe, quien tiene gran parte de la responsabilidad de hacer realidad estos productos, desde su concepción hasta el ensamblaje. Esto fue lo que nos dijo.
GUILLERMO LIRA: ¿Cómo le ha ido durante la pandemia, especialmente considerando que su equipo en Glashütte es grande y estuvieron separados?
TINO BOBE: El primer año no resultamos tan afectados ni pasó nada grave en realidad. Durante el segundo año, el impacto fue más significativo, sobre todo en la ola causada por la variante ómicron. En uno de nuestros departamentos con 12 personas, había días en los que solo trabajaban tres. En general, estamos satisfechos con los resultados de este año, pero estuvo lleno de retos. Porque si haces trabajo de oficina, puedes seguir desde casa, pero si te dedicas a pulir, ensamblar o producir componentes, no hay otra opción que trabajar desde el taller. Adoptamos todas las medidas posibles, para, por lo menos, disminuir el riesgo de contagio de los empleados en sus horas laborales, lo cual funcionó bastante bien.
GL: ¿Cuántos años lleva en Lange?
TB: Empecé en 1999, así que ya van 23 años.
GL: Como uno de los tres ejecutivos más importantes de la manufactura, ¿qué tanto abarca en su misión de producción y cuántas personas tiene a su cargo?
TB: Desde 2014, nuevamente me encargo de toda la manufactura, es decir, de las partes de producción directas e indirectas. Tenemos un departamento fuerte que produce todos los componentes y contamos con diferentes tipos de máquinas, por ejemplo, máquinas de electroerosión. En el área trabajan unas 73 personas. También tenemos más de 50 personas en el departamento de acabados a mano, con la responsabilidad de resaltar la belleza de todos los artículos a través del pulido, de granear los relojes, de las pulseras y los grabados. Además, está el departamento donde se ensamblan los relojes, con más de 160 relojeros, que es mi personal directo de producción.
Asimismo, tenemos el personal indirecto de producción. Es el departamento de logística, el de calidad, el de tecnología. Considerando todo esto, mi equipo consiste en aproximadamente 400 de las 600 personas que están en [la Manufactura de] Glashütte, incluyendo el personal de finanzas, otros departamentos y los trabajadores en capacitación.
Por otro lado, soy parte de un equipo reducido, formado por el señor Wilhelm Schmid [CEO], Anthony de Haas [director de desarrollo de producto] y yo. Somos responsables de los productos, de la estrategia y el portafolio del desarrollo del producto. Si no tuviéramos esta relación cercana entre Tony de Haas y yo, no podríamos empujar los límites para crear productos nuevos e interesantes con esta frecuencia, y presentar de dos a tres movimientos cada año. Trabajamos con 31 diferentes movimientos este año de manera paralela en la producción para tener nuestro portafolio de productos completo. Se podrá imaginar lo que implica esto para nuestra organización. Tenemos un poco más de 70 referencias y producimos más o menos 5,000 relojes. ¿Se imagina cómo hay que organizar este flujo, para que todo funcione?
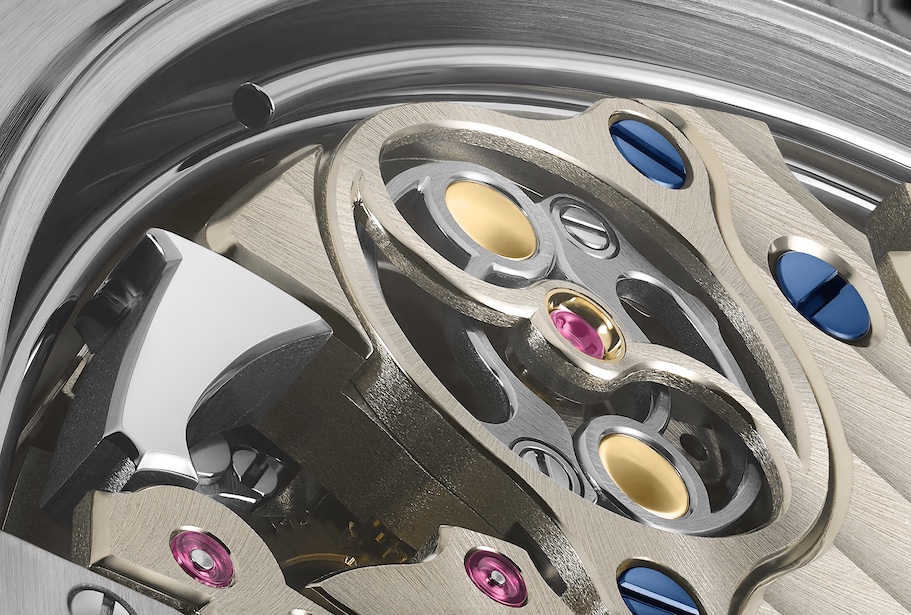
Los martillos y gongs del Richard Lange Minute Repeater.
GL: Tiene un departamento lleno de retos. Todos sus empleados tienen conocimientos muy especializados, su trabajo es altamente especializado. ¿Cómo resuelve este problema?
TB: Desde los años 90, cuando me uní a la compañía, teníamos nuestra escuela de relojería. Empezamos con tres personas por año. Actualmente, son alrededor de 10 a 12 personas por año. El ciclo de su aprendizaje dura tres años. De esta manera, creamos nuestro propio futuro en términos del personal capacitado, formados para nuestras necesidades. De otra forma, no existe un mercado para relojeros en Alemania o en nuestra región. Así, si queremos crecer como empresa, nuestra capacitación es la única manera de formar nuevos relojeros. Cada año, unos dos o tres relojeros se jubilan, un par de personas jóvenes deciden continuar con sus estudios, y nosotros acabamos con cinco o seis personas, mientras nuestro portafolio se vuelve más complejo cada año. Significa que necesitamos más relojeros incluso si la cantidad de los relojes permanece estable. Si los relojes tienen más partes para ensamblar, se vuelven más complejos; en consecuencia, necesitamos más personas con este conocimiento.
Si se fija en el nivel de complejidad de nuestro portafolio, viendo relojes como el Tourbograph, el Minute Repeater, todos los cronógrafos y el cronógrafo con calendario perpetuo, entre otros, se da cuenta de que necesitamos muchos relojeros altamente capacitados para estos proyectos.
GL: ¿Ha incrementado la producción del Odysseus? En términos del volumen o de la complejidad de la línea de producción…
TB: El movimiento está a la mitad de la complejidad de nuestro portafolio, debido a los discos que indican el día de la semana y la fecha. No es un movimiento fácil. Es un movimiento de 312 piezas. Para comparar, el Saxonia Thin tiene 164 piezas. No aumentamos el número de relojes en su totalidad, más bien tuvimos que reducir nuestras familias. Tenemos 31 diferentes movimientos para 5,000 relojes. Usted puede calcular el grado de exclusividad.
GL: Hablando de los repetidores de minutos, ¿cuántos produce al año? Ustedes son parte del sector exclusivo de la relojería fina. Ahora que vemos el nuevo Richard Lange Minute Repeater, ¿cuáles son sus expectativas para la producción de este reloj?
TB: Para nosotros, es muy importante producir y entregar al cliente los relojes limitados dentro de un periodo de dos a dos años y medio. Si el cliente tiene que esperar más, no lo considero justo. El Grand Complication es la única excepción que hicimos; tomamos la decisión de elaborar seis relojes para entregarlos dentro de cinco años. Sin embargo, fue un caso excepcional. Pensamos que, si podemos producir uno al año, en un periodo de cinco años podríamos producir uno adicional, y así seis en total.
En este momento, tal vez podríamos hacer 20 repetidores de minutos al año, lo que se traduce en producir dos por mes. Entregaríamos estos 50 relojes de edición limitada en un plazo de dos años y medio.
GL: Se puede decir que tiene la capacidad de producir un Minute Repeater cada 15 días, ¿es correcto?
TB: Tal vez lo podemos decir así. Tenemos entre 20 a 22 días laborales al mes. Creo que se necesitan 10 a 12 días para hacer uno de estos repetidores de minutos, tan solo para ensamblar, para probar, para la labor de un relojero. Muchas personas más tienen que trabajar para producir los componentes, para optimizar el artículo. Desde 2013, cuando lanzamos el Grand Complication, hemos obtenido experiencia con el indicador de tiempo acústico y, gracias al apoyo externo, ahora podemos realizar mediciones de precisión para optimizar, pero esto toma tiempo.
GL: Entonces, se producen 20 repetidores de minutos al año. ¿Cuántos relojeros tiene que ensamblan el reloj?
TB: Si contamos a todas las personas capaces de hacerlo, realmente los relojeros con mucha experiencia son cuatro, pero también tienen que elaborar Tourbographs, entre otros relojes. Entonces, en realidad puedo encargar esta tarea a dos personas. Si estas dos personas están de vacaciones o de incapacidad, 20 al año puede ser una cifra desafiante para nosotros. Creo que todavía nos falta hacer unos 12 a 14 tipos de repetidores de minutos al año.
Cuando Anthony me presenta sus ideas, en realidad revisamos juntos qué es factible. A veces, le puedo decir que las limitaciones en este reloj llegaron a su fin, en este caso seguimos a un nuevo reloj. Realmente colaboramos estrechamente para organizar este flujo. Sería una pena tener los relojeros maestros y nada que pedirles a los relojeros, solo porque el desarrollo no está listo en este momento. Serían unos meses o un medio año en los cuales les pides a tus relojeros cosas regulares. Y, por el contrario, no los puedo duplicar artificialmente.
Siempre buscamos capacitar más personas jóvenes que elaboran piezas más simples, que empiezan desde el Saxonia, Lange 1 u Odysseus, y después continúan al departamento de las complicaciones. Siempre se requiere de talento para convertirse en un maestro relojero, pero el talento por sí solo no es suficiente. Es como en la pirámide de los deportes: tienes los deportistas de talento, pero también necesitan tener la fuerza mental para lograr sus metas, porque no es tan fácil.
GL: ¿Qué tan complejo en términos de la producción es el nuevo Odysseus que presentaron este año?
TB: Sigue siendo el mismo bello movimiento que conocen. Representa la elegancia deportiva, puede tener un uso deportivo, aunque no es un reloj deportivo en sí. Nos esforzamos en resaltar el titanio como un nuevo material para la pulsera y para la caja. Pensamos mucho en cómo hacer el acabado para resaltar su belleza. El reloj es un poco más ligero, 104 gramos ahora, en comparación con 148 gramos. Queríamos aprovechar esta diferencia y su ligereza. Para hacerlo, era crucial saber cómo realizar el acabado del reloj, y esta búsqueda tomó más de un año. Porque, adicionalmente, tuvimos que acabar todas las piezas pequeñas de la pulsera por separado. No lo puedes hacer después, realmente necesitas hacerlo componente por componente para encontrar de qué manera se ve perfecto. La perfección está en el detalle.
GL: ¿Cuáles son los retos para la relojería para los próximos seis años? Considerando la disrupción de la logística, los nuevos materiales, la industria reactivándose…
TB: Uno de los retos es asegurarnos de que cada año tengamos un número suficiente de personas jóvenes con ganas de hacer la capacitación en la relojería que le comenté. Muchas personas no viven en Glashütte o en los alrededores, sino vienen desde Dresde. Aparte, hay otras empresas grandes, tales como Siemens o Bosch, que también están en búsqueda de trabajadores jóvenes. La cantidad de jóvenes que salen de las escuelas está disminuyendo ligeramente. En este contexto, realmente tenemos que hacer un esfuerzo para mostrar lo que hacemos, para mostrar que es un negocio fascinante, y así atraer a los jóvenes. Porque, ya sabe, los jóvenes a veces quieren ser youtubers o dedicarse a algo digital.
Otro reto es claro si se fija en nuestras líneas de producción. Tenemos que elaborar este algoritmo/transición de las tareas más simples a las tareas más complejas, porque las tareas tienden a aumentar en complejidad. Es nuestro placer producir estas bellas complicaciones. Cada año surge algo interesante en términos de complicaciones. Nuestros clientes lo esperan de nosotros, ya que la mayoría de nuestros clientes son coleccionistas. Siendo coleccionistas, dudo que vayan a comprar un quinto Lange 1. Ellos buscan relojes más complicados. Y, al mismo tiempo, no significa que no necesitemos Lange 1. Al contrario, es muy necesario y esto se refleja en nuestra colección de este año.
GL: ¿Su reloj favorito este año?
TB: Es una pregunta muy difícil. Para mí, debe ser el Minute Repeater. Estoy fascinado. Si el Minute Repeater está activado, el gobernador gira a una velocidad de 2,000 revoluciones, lo cual garantiza la cadencia uniforme de los golpes.
Entrevista realizada en Ginebra bajo el marco de Watches and Wonders en el espacio de la manufactura, por video conferencia por la cuarentena que el entrevistado tuvo que guardar esos días por la pandemia Covid 19.